Inside the Kohler Co. pottery, where workers cast and fire clay into sinks, toilets and tiles on an industrial scale, Sharif Bey makes ceramic pieces for large, sculptural headdresses.
He’s one of 12 artists in the Arts/Industry residency, run by the John Michael Kohler Arts Center in Sheboygan. The annual program grants artists 24-hour access to Kohler equipment and materials in its pottery, the part of the factory that uses clay, or the foundry, where iron is cast. An on-site technician assists residents and serves as a bridge between artist and factory.
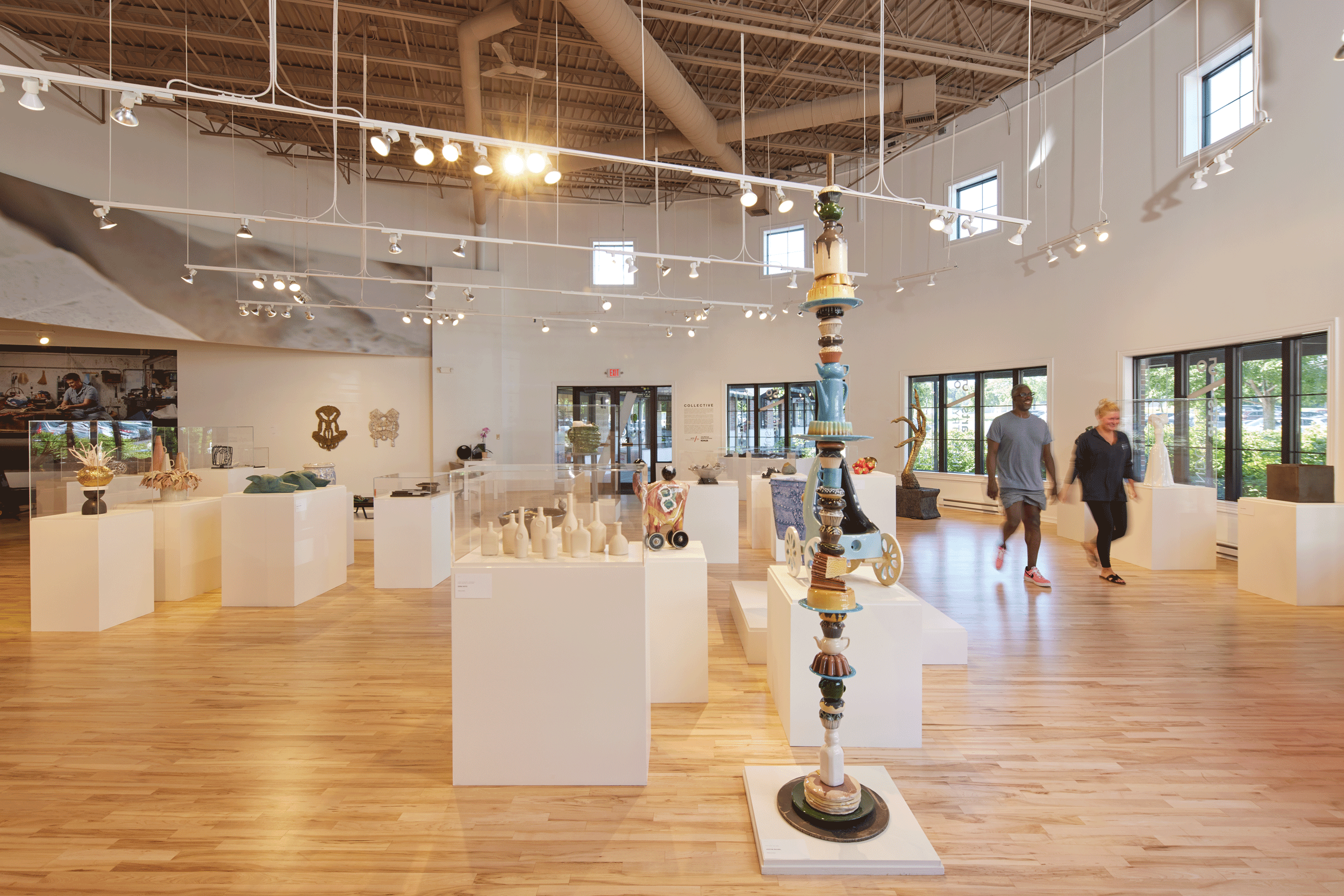
Over three months, residents gain a body of new work and invaluable skills and practical knowledge. In turn, Kohler workers get an opportunity to think creatively, experiment and, it’s hoped, innovate.
Ruth DeYoung Kohler started Arts/Industry 50 years ago, in 1974, to provide an opportunity for manufacturing and art-making to learn from and inspire each other. Now, throughout this year, the Kohler Arts Center is celebrating the anniversary with workshops and exhibitions recognizing the program’s impact on both sides.
“It’s an incredibly holistic approach, showcasing the work that happens behind the factory and then bringing it into the gallery space,” says Arts/Industry program director Siara Berry. The Kohler Arts Center forwent the usual application process for this year’s cohort, instead inviting an even mix of alumni and newcomers for a more curated approach.
“You don’t really turn something like this down, especially if you were invited,” says Sahar Khoury, a sculptor who’s a first-time Arts/Industry resident. As of June, she’s creating molds of foods like strawberries and pita bread to capture their textures and spark thought about food origin and sovereignty. “I think I’m here to cast as much as I can to then take with me and incorporate into other work.”
Bey always hoped to return. This is his second Arts/Industry residency, his first being a five-week stint in 2014. Then, he took advantage of the pottery’s reusable molds to cast many parts for necklaces. “Those works were pivotal for my career,” Bey says. “Every cast that I made 10 years ago is in a museum today.”
Bey came into his second stint “to take the time to do something more grand and experimental,” he says. Both he and Khoury don’t normally plan out projects, but working in the factory has made them think ahead.
And unlike other residencies, the artists are guests in a space not dedicated to them. “There are certain things that are detrimental to the production, and they have to be approved,” Bey says.
Kohler workers aren’t making art with the artists, but they answer questions and give one-on-one technical support. To Khoury, learning a craft this way resembles an old-school apprenticeship.
“It could only have been devised by an artist, and then one who also was familiar with industry,” Khoury says. “That pairing, I wish [it] would exist more. I think we’d have better products in this world. I think we’d have better artists.”
Arts/Industry residents will talk about their experiences at the John Michael Kohler Arts Center on Aug. 10 from 2-4 p.m. Sharif Bey’s work during his residency will be shown at the John Michael Kohler Arts Center in early December.
Foundry or Pottery?
During the application process, Arts/Industry residents choose between two factory spaces in which to explore and create art. In the pottery, artists work with a clay body called vitreous china that they cast, fire and glaze. Reusable casts allow for the same object to be created in multiples.
In the foundry, artists use cast iron and create with resin-bonded sand casting. The larger and heavier works mean less room for error. “It’s harder to actually get access to a place that does it, so that’s why I picked it,” Khoury says.